燒焦是指在注塑加工過程中由于模具排氣不良或注射太快,模具內(nèi)的空氣來不及排出,則空氣會(huì)在瞬間高壓下急劇升溫,而將熔體在某些位置燒黃燒焦的現(xiàn)象。那么怎么去呢?
Charring refers to the phenomenon that the air in the mold cannot be discharged due to poor exhaust or injection too fast in the process of injection molding, and the air will heat up rapidly under the instant high pressure, and the melt will be burnt yellow and charred in some positions. So how to solve it?
末端注射速度過快:降低比較靠后的一級(jí)注射速度。
Too fast terminal injection speed: lower the injection speed of the lower first stage.
模具排氣不良:加大或增開排氣槽(抽真空注塑)。
Poor exhaust mold: increase or open exhaust groove (vacuum injection molding).
注射壓力過大:減小注射壓力(可減輕壓縮程度)。
Injection pressure is too high: reduce the injection pressure (can reduce the compression degree).
熔料溫度過高(黏度降低):降低熔料溫度,降低其流動(dòng)性。
The temperature of the melt is too high (viscosity is reduced) : the temperature of the melt is reduced and its fluidity is reduced.
澆口過小或位置不當(dāng):改大澆口或改變其位置(改變排氣)。
Gate too small or improperly positioned: change the gate or change its position (change the exhaust).
塑膠材料的熱穩(wěn)定性差(易分解):改用熱穩(wěn)定更好的塑料。
Poor thermal stability of plastic materials (easy to decompose) : switch to plastic with better thermal stability.
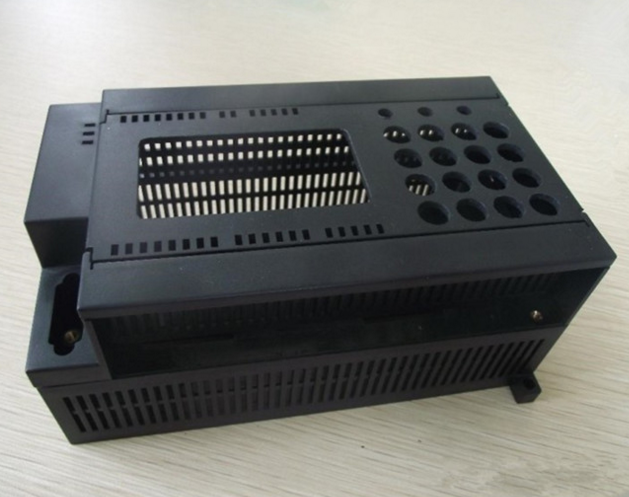
可能是溶體破裂導(dǎo)致燒焦,當(dāng)熔體在高速,高壓條件下注入容積較大的型腔時(shí),極易產(chǎn)生熔體破裂現(xiàn)象,此時(shí),熔體表面出現(xiàn)橫向斷裂,斷裂面積為粗糙地夾雜在塑件表層形成糊斑。特別是少量熔料直接注入容易過大的型腔時(shí),熔體破裂更為嚴(yán)重,所呈現(xiàn)的糊斑也就越大。
When the melt is injected into the cavity with large volume at high speed and high pressure, it is easy to produce the phenomenon of melt rupture. At this time, transverse fracture occurs on the surface of the melt, and the fracture area is coarsely mixed in the surface of the plastic parts to form paste spots. Especially when a small amount of melt is directly injected into the cavity which is easy to be too large, the melt rupture will be more serious and the paste spot will be bigger.
濟(jì)南注塑加工成型條件控制不當(dāng)導(dǎo)致燒焦一般情況下,層流形成的塑件表面較為光亮平整,紊流條件下形成的塑件不僅表面容易出現(xiàn)糊斑,而且塑件內(nèi)部容易產(chǎn)生氣孔。因此,注射速度不能太高,應(yīng)將流料控制在層流狀態(tài)下充模。如果熔料的溫度太高,容易引起熔料分解焦化,導(dǎo)致塑件表面產(chǎn)生糊斑。
Ji 'nan injection molding conditions caused by improper control of burning in general, laminar flow formed the surface of the plastic parts is bright and smooth, turbulent flow conditions formed under the plastic parts are not only easy to appear on the surface of the paste spot, but also easy to produce pores in the plastic parts. Therefore, the injection speed should not be too high, and the flow material should be controlled in the laminar flow state. If the temperature of the melt is too high, it is easy to cause the decomposition and coking of the melt, resulting in paste spots on the surface of the plastic parts.
濟(jì)南注塑加工過程中出現(xiàn)燒焦的問題到此講解完畢了,如果您還有其他方面的問題要了解的話,可以來我們網(wǎng)站
www.szhouyuan.com咨詢下!
Ji 'nan injection molding process in the burning problem to the end of this explanation, if you have other problems to understand, you can come to our website www.szhouyuan.com consultation!